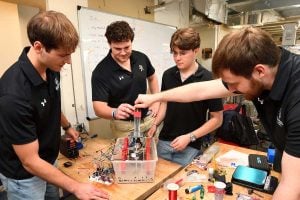
Someday, a mechanical engineering student team’s robotic device may be testing soil on the Moon. But for now, it’s being deployed in more terrestrial areas, like the senior design space in the Wyman Park Building.
“That’s Earth samples—aka parking lot dirt,” explained team member Xander O’Malley, pointing to a bin filled with what looks like regular beach sand. “It’s just a preliminary test medium.”
The sand is acting as a rough simulation of lunar soil—something which hasn’t been tested since the Apollo missions in the 1970s. Sponsored by Johns Hopkins Applied Physics Laboratory (APL), O’Malley and team members Aidan Green, Matthew Konkol, and Alexander Pivovarov are working on a device that could, once we get back to the Moon, make testing soil easier and quicker than it was half a century ago. For the hardcore testing and exact data collection, the team is using LHS21E lunar simulant.
The students will present their project April 29 at the Whiting School of Engineering’s Design Day in the Ralph S. O’Connor Recreation Center and April 30 at the department’s senior design event at the Pava Center— annual events showcasing students’ solutions to real-world problems.
“The Apollo tests were basically done with an astronaut using a huge stick and pushing it into the ground,” explained Pivovarov. “It wasn’t an efficient procedure and could only measure two things. To do more thorough testing, samples needed to be brought back to Earth. But that won’t be the case next time.”
The team’s device can measure a lot more than bearing strength and shear strength—the only two properties the Apollo crews could readily test. It would immediately determine additional properties like temperature and permittivity (opposition to an electric field). And being fully autonomous, it could be attached to roaming vehicles exploring previously unvisited lunar locations.
“Every test that has been done so far has been on the lunar mare (plains areas), of the Moon,” Pivovarov said. “We are designing for testing on the highlands, where conditions are much harsher. It’s uncharted territory.”
But what lies in that uncharted territory? The Apollo missions revealed that, without wind, water, or erosion on the Moon, particles remain more abrasive and geometrically jagged. Lunar sand, called regolith, ranges from silt- to gravel-sized. Using synthetic regolith—and parking lot dirt—the team aims to develop a device that can reliably dig and navigate in different types of soil, complete instant testing and analysis on the spot.
“There are many different layers of soil, and we haven’t really tested the deeper ones,” said O’Malley. “The challenge is to do everything on the Moon: No need to send samples back.”
The area between about 5 and 11 cm is the sweet spot for lunar soil testing. The reason? It provides valuable data about the soil’s load-bearing capacity—information crucial to understanding is ability to support vehicles, structures, and other loads.
“Our main goal is getting all the knowledge we can from the soil, but the secondary goal is being able to build structures on the moon,” Konkol said.