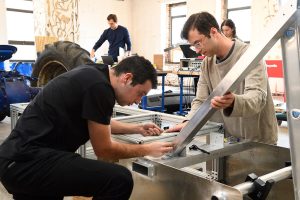
Forklifts are known for their maneuverability and ability to move large objects—not their speed. While you probably won’t see a forklift race any time soon, speed is still a variable that must be considered. When handling heavy loads with uneven weight distribution, maintaining the correct pace is a safety requirement to prevent dangerous tipping.
Oceaneering, a Houston-based robotics company, designs and sells autonomous forklifts. Unlike human drivers, these machines can’t adjust their speed based on” feel”—so the company asked Hopkins mechanical engineering students to develop a system that could.
The student team will present its solution—an algorithm that enables Oceaneering’s sizeable forklifts to optimize their speed according to load size and height—at the Whiting School of Engineering’s Design Day showcase on April 29 and 30.
“What (Oceaneering) wanted from us was essentially to create a real time scale under each wheel to find out where the center mass of the forklift is at all times and determine how fast we can safely drive without falling over,” said team member Rachel Fox, a senior in mechanical engineering. “Currently, they program the autonomous forklifts to drive slowly and carefully to avoid tip overs. They want to push the design boundaries a little bit more so the equipment can safely move faster, increasing productivity.”
Because the students lacked access both to a physical forklift and a license to operate one, team members Fox, Sam Cohen, David Hindman, and Charlie Margulies built a scale model of Oceaneering’s MaxMover—a three-wheeled forklift—in the Senior Design space in the Wyman Park building on the Homewood campus.
“We built a metal rectangle frame with an internal structure that simulates theirs, with wheels and a mechanical arm that mimics theirs,” Fox said. “We also placed load sensors at specific locations on our model forklift to take direct-strain measurements.”
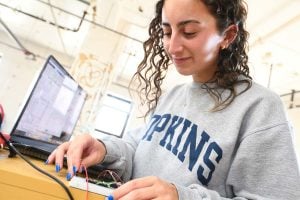
“My teammates have done a lot of design work in making that structural test frame, but my work has been mostly in designing the sensors.”—Rachel Fox
To get those measurements, the team used strain gauges—small devices that are adhered to the material being tested. Stretching or compressing that material results in electrical signal changes that indicate how much force or weight is being applied in real time.
“We’ve created prepackaged, prewired kits that we can put directly on the hardware,” Fox said. “We’ve also walked on the test bed and placed barbell weights on the test bed—we’ve had to get pretty creative. There was a big learning curve on figuring out how the gauges work and how to install them and all the things that can go wrong with them.”
These tests measured how the varied distribution of weight affected the forklift’s center of gravity. The student engineers then fed that information into their computing software, tweaked their calibrations, and created an algorithm that could determine how fast a forklift could safely travel with a certain load without tipping over.
The multi-stage project has incorporated several engineering disciplines—a hallmark of mechanical engineering.
“What’s interesting about this project is that it’s a little bit more about electronics and sensor space than a large design,” Fox said. “My teammates have done a lot of design work in making that structural test frame, but my work has been mostly in designing the sensors.”
Fox said they plan to test the team’s design in Oceaneering’s plant before the semester concludes. Their ultimate goal is for their design to be put to use in Oceaneering’s forklifts.
“It’s a fairly simple algorithm: specific to their forklift and their situation,” Fox said. “In the end, they want to be able to have a small system that they could just retrofit onto any forklift.”
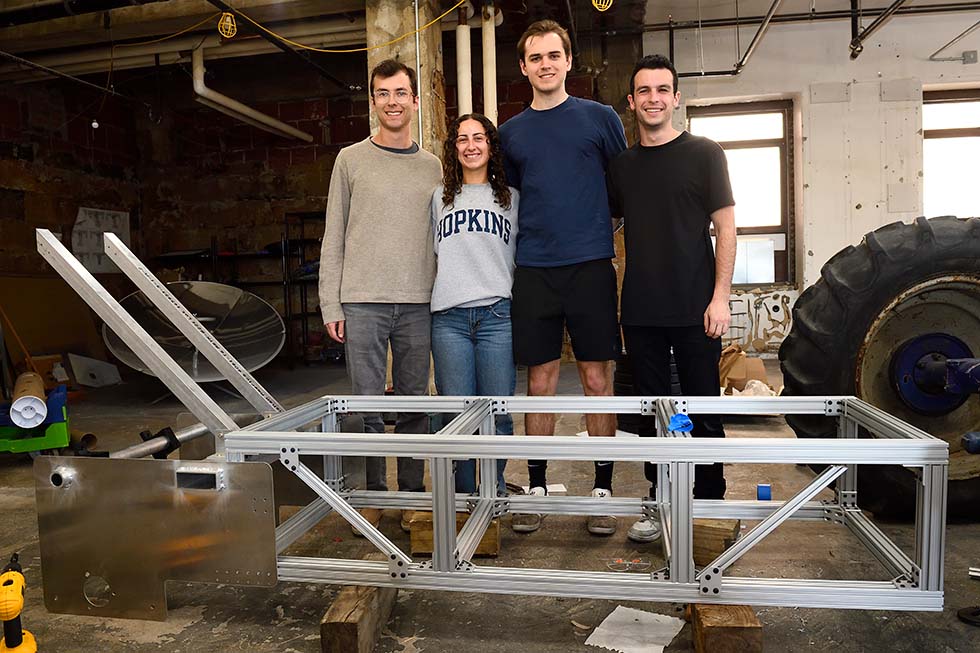
The OCEAN25 team with their partially-completed forklift simulation. L to R: Charlie Margulies, Rachel Fox, David Hindman, Sam Cohen.