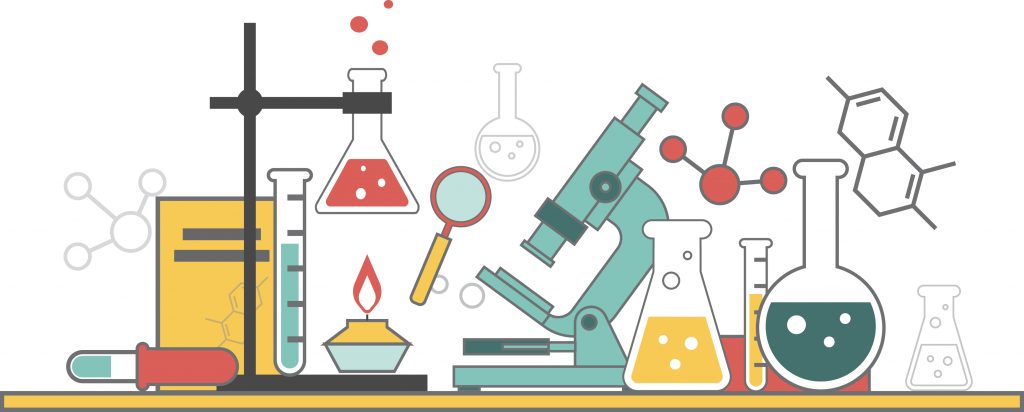
Unlike traditional drugs, which have been manufactured in much the same way for more than a century, purely through chemistry, biopharmaceuticals are drugs made in living cells.
For example, they’re the innovative monoclonal antibodies that have made great strides against cancer in recent years and the vaccines such as the one produced each season for the flu.
Producing drugs in living systems has given new hope for treating diseases for which there were previously no effective therapies. However, says Michael Betenbaugh, professor in the Whiting School’s Department of Chemical and Biomolecular Engineering, production can be challenging and expensive.
As an expert in these techniques, Betenbaugh was tapped last year to co-direct the Advanced Mammalian Biomanufacturing Innovation Center (AMBIC). A collaboration between the National Science Foundation and four universities— including Johns Hopkins—AMBIC’s goal is to develop new technologies to improve biomanufacturing of drugs from living organisms, such as Chinese hamster ovaries or other mammalian cells.
Betenbaugh’s work doesn’t stop there.
In early 2016, when the National Institute of Standards and Technology launched an “open topic” competition for a new institute to solve any industry-relevant manufacturing challenges, he was up for a new challenge. Working with longtime collaborator Kelvin Lee at the University of Delaware, also a director of AMBIC, the two assembled fellow academics and industry experts to develop a proposal. By mid-December, NIST announced the team’s idea—the National Institute for Innovation in Manufacturing Biopharmaceuticals (NIIMBL)—as the winner.
Unlike AMBIC, which takes on high-risk, early-stage projects, NIIMBL will focus on finding the best ways to implement ideas that have already proven useful in the lab. With $70 million in federal funding and another $180 million investment from other stakeholders, the new institute will combine the expertise of Johns Hopkins and other academic institutions, industry, and government organizations to fine-tune existing biopharmaceutical manufacturing techniques.
“What this means for patients is the potential for new, better, and less expensive biopharmaceutical drugs to be accessible sooner,” Betenbaugh says. “It’s all about making health care more effective and efficient in our country through innovative manufacturing practices.”