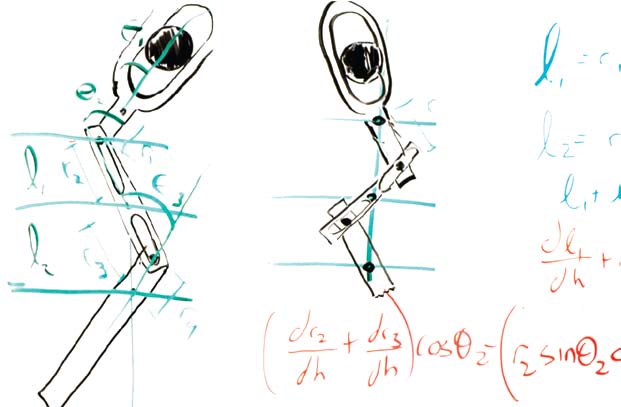
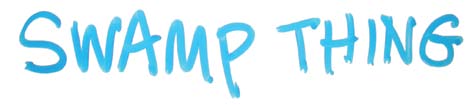
Tropical fish enthusiasts prize the black ghost knifefish, a jet black river dweller from South America marked by two white rings on its tail, a white blaze on its nose, and a long undulating fin running along its belly. That fin—called a ribbon fin—allows the fish to hover or advance or change direction almost instantaneously by propagating different waveforms down the length of its underside. So effective is this mechanism that the fish catches its food by gliding past unwary targets and then suddenly changing course and attacking in the blink of an eye: up, down, forward, back, or side to side.
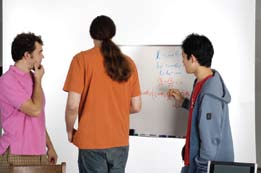
Watching one of these knifefish pivot through the water can be an amazing sight (check out the dozens of black ghost knifefish home videos on YouTube to see), but it was also bound to get scientists thinking …can we design an underwater vehicle to do that? And so the quest was on for SWAMP, the Submersible Wavelength/Amplitude Modulating Propulsion system. Scientists in Japan and at Northwestern University have already had a go at it. Now enter Johns Hopkins Team SWAMP—mechanical engineering majors Chris Blizzard, Ross Burns, and Makibi Takagi—with a uniquely different approach to the challenge.
“This kind of system underwater could allow far greater maneuverability than a standard propeller.” Ross Burns
“Nothing like this had been tried before,” says Burns. The other groups tackling the problem started with a parallel row of closely-spaced rods that approximate the bones in the fish’s ribbon fin. But while the Japanese and Northwestern groups utilized a series of independent actuators to move each rod back and forth, Team SWAMP took a more traditionally mechanical engineering approach, utilizing revolving shafts linked to a row of 18 parallel plastic bars. A complex system of gears and actuators link the shafts to independent electric motors that can be used to vary the speed and direction of the bars’ movement. A third shaft controls the amplitude (the height of the wave motion) by raising or lowering the fulcrum point for each bar. The entire unit is controlled by a variable power supply and a simple switching circuit.
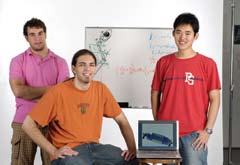
“This kind of system underwater could allow far greater maneuverability than a standard propeller,” Burns says of the prototype he and his classmates designed, machined, and assembled themselves. “The hardest challenge for the team was actually putting it together. We had to build it and rebuild it several times to get it to work.” At one point the group fell behind schedule by more than a month when gears on parallel shafts refused to mesh properly and the mechanism seized. Team SWAMP’s final report notes tersely: “It was then that the panic set in.” In the nick of time the group entirely redesigned the base unit, which effectively eliminated the problem and allowed work to resume. There were many long nights in the lab getting the device in working order, but in the end, they had a functioning prototype for their project sponsors to test drive. “They were in awe that we were able to do it,” says Burns with a trace of pride bordering on relief. “The greatest thing we learned was how to take ideas and actually make them real.”
Team sponsor: Applied Physics Lab through a Navy research grant