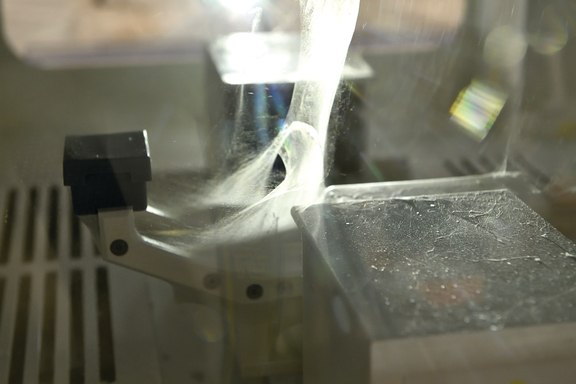
When the COVID-19 pandemic made its way to the United States, Stephen Farias, PhD ’14, began thinking of ways to help.
As director of engineering at DiPole Materials, an electrospinning company in the Baltimore neighborhood of Pigtown, his mind immediately jumped to the company’s Elmarco machine, which creates electrospun nanofibers for commercial prototyping or small-scale production. The machine, he realized, is also capable of manufacturing nanofibers with filtering capabilities similar to those of an N95 mask.
DiPole’s representatives pitched the project to investors and quickly received the funding they needed. The last piece of the puzzle was who would do the actual labor. To make as many filters as possible, the Elmarco machine needed to run 24 hours a day, which would overburden DiPole’s full-time staff.
DiPole put out a call to students from local colleges, asking if anyone with experience handling chemicals would like to help. The group received an overwhelming response, particularly from Johns Hopkins students. In total, 13 current students and graduates from the Whiting School of Engineering and Krieger School of Arts and Sciences began working on the project.
Though the project features students from a number of local colleges, the sizable contributions from Johns Hopkins students is just the latest in a history of collaboration between the university and the company. James West, a professor of electrical and computer engineering at the Whiting School, helped co-found DiPole in 2015, and the company’s first piece of technology originated in his lab. In addition to Farias, the company has hired multiple Johns Hopkins alumni in recent years.
The majority of the Johns Hopkins students perform quality control for the project, ensuring that the material being produced by the Elmarco machine meets filtering specifications.
“We make enough material for about 2,000 mask filters per day,” Farias says. “Once the filters are created, we send fabric rolls of our materials to other [mask] manufacturers that put it into the final mask products. We are distributing to several local mask fabrication companies, as well as some large local and domestic textile manufacturers.”
Other Whiting School alumni who have joined Farias on the project are Matthew Davenport ’13 and James Shamul ’17, MS ’18.