Todd C. Hufnagel remembers the day he first heard of metallic glass. As an undergraduate at Michigan Technological University in the late 1980s, where he majored in metallurgy, he read a textbook passage that described this unusual material. That ignited a keen interest, which Hufnagel eagerly has pursued at the Whiting School as an assistant professor of Materials Science and Engineering.
Metallic glasses (also called amorphous metallic alloys) weren’t even developed until 40 years ago. They aren’t a glass in the general sense of the word. They’re not brittle. They’re not even clear. They’re springy, and can be molded into complex shapes. Add iron to the alloy, and the metallic glass gains very useful magnetic properties.
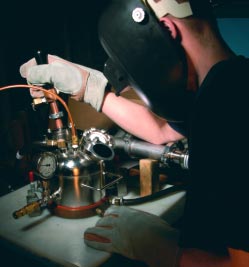
Today, as a result of the research of Hufnagel and his team over the past seven years, his lab exploring these novel materials has gained a reputation as one of the premier research centers for the study and actual manufacture of bulk metallic glasses. The “bulk” part (as in ingots) has been a special challenge for researchers, because for many years these novel alloys could only be made into thin ribbons, wires, or powders.

Hufnagel has been creating metallic glasses by experimenting with various hybrid alloys, using zirconium, titanium, nickel, and other metals. Pure metals in their solid state are crystalline, with their atoms arranged in a uniformly organized pattern or lattice. However, in a liquid state, metallic atoms lose this orderly arrangement, becoming jumbled or amorphous in structure, like the “frozen liquid” state that is characteristic of a glass. However, as they cool, most metals will recrystallize. But if they’re cooled quickly enough, they can retain their amorphous properties even as a solid at room temperature.

It’s fairly simple to create such amorphous solids as silicate (window) or polymer glass. In fact, the Egyptians first made glass coatings from sand 6,000 years ago. But creating glass from metals is another matter entirely. To create a glass from a pure metal such as nickel or copper, the cooling rate would need to operate at about 1 trillion degrees C. per second, so most scientists dismissed the process as impossible. Then, by the 1960s, metallurgists at Cal Tech had discovered they could produce metallic glass by cooling thin layers of hybrid alloys at only 1 million degrees C. per second. But given the stringent production requirements involved, only small amounts of metallic glass could be created.
“I read that metallic glass had these interesting properties, but the limitation was that they had to be made in very thin strips,” recalls Hufnagel. “I remember even at that time thinking, ‘Gee, wouldn’t it be cool if you could make a bulk sample or an ingot of a metal that was still in this glassy state.’ I filed this thought away in the back of my mind, and didn’t expect anything to come of it.”
Fast-forward to the early 1990s. After earning his PhD in materials science and engineering from Stanford University, followed by a two-year teaching stint there, Hufnagel began searching for a full-time faculty position. In the fall of 1996, all of the puzzle pieces fell into place. Around the time the Whiting School hired him, Hufnagel was reading about new metallic glassy alloys that could be produced in bulk samples, due to lower cooling rates. The light bulb lit up. “It rekindled my interest in that whole field,” he recalls. “Just when I was about to start a new research program, the area that had attracted me 10 years earlier was now available for me to study. It was a very serendipitous occasion.”
In Control of All Phases
“Todd is an outstanding researcher and one of the pioneers in the area of bulk metallic glasses,” according to Peter Searson, chair of Materials Science and Engineering at the Whiting School. “He brings to Hopkins a unique expertise that exists in relatively few labs worldwide.” Searson points out that Hufnagel’s “soup-to-nuts” capabilities give his lab a critical edge. “Other research groups around the world are studying these materials but lack the capabilities to make them,” Searson notes. “But Todd is able to do everything—he has control over the making of his metallic glasses in the amounts he wants.” His lab has even been able to make metallic glasses at cooling rates as low as 1 degree C. per second.
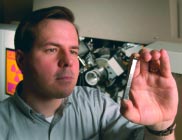
Maintaining this lead position is key in the current research race to transfer the unusual properties of metallic glass to real-world applications. Because it melts at relatively low temperatures, metallic glass can be cast easily into complex shapes. While hard, it possesses an amazing degree of “springiness,” which generates a high degree of bounce in response to any surface impact. No wonder metallic glass is being used in premium golf club heads! NASA’s Genesis spacecraft, in collecting samples of solar wind particles, is employing collector arrays made with bulk metallic glasses. Other applications being explored include cases for cell phones and other electronic equipment, precision medical instruments, and armor-penetrating projectiles.
Hufnagel’s research is supported by the U.S. Department of Energy’s Office of Basic Energy Sciences, the Army Research Laboratory, and the National Science Foundation.
Master of the Milestones
Located in Maryland Hall, Hufnagel’s lab has already passed several important research milestones. The first was learning how to make the material within a controlled environment. “It’s not easy,” the metallurgist admits. “There are tricks of the trade, and processing has to be done very carefully.”
A second big step came with the lab’s creation of a new type of metallic glass alloy that is embedded with tiny particles of a soft crystalline, metallic material. “This alloy has superior properties to regular metallic glass, which can fail in a brittle manner,” says Hufnagel. “The addition of these particles goes a long way to solving that problem—and gives us a lot of flexibility in the kinds of things we make.”
A third milestone involves ongoing research into the mechanical properties of metallic glasses, in terms of their strength and how they deform. Because metallic glasses are composed of randomly arranged atoms, they deform on an atomic scale in a very different way than crystalline metals do. “We’ve made some fairly important contributions to understanding that mechanical process by using electron microscopy to study the structure of these deformed glasses on the atomic scale,” Hufnagel says.
Despite all of the advances he and his lab team have made to date, Hufnagel believes he has only started to scratch the surface of metallic glasses. “We’ve just begun to explore the range of possibilities of what we do with those structures. As with all interesting research, the things that we’ve done raise more questions than answers,” he says. “Now we’re starting to address those questions.”
Visit Todd C. Hufnagel’s web site at www.jhu.edu/~matsci/people/faculty /hufnagel/hufnagel.htm