Benjamin W. Schafer admits that some fellow researchers around the world consider him “a little odd.” Flying in the face of traditional academic practices, for the last six years the assistant professor of Civil Engineering at the Whiting School literally has been giving away his research.
In fact, he urges designers of thin-walled structures to download his software directly from his web site. He wants them to plug in what materials they’ll be using, the expected load, and the geometry of the structure they’re planning to build—for example, box girder bridge, building, culvert, or pipe. Then his modeling software will tell them whether or not their structure will buckle and collapse—all for free.
If he’s crazy, it’s like the proverbial fox. By releasing online his free software program, Schafer quickly has gained international stature as an authority in this area of structural engineering. “Ben is part of a new generation of researchers trying to get results out into both the marketplace and the research environment, so that other people can take advantage of what he’s found,” according to Robert A. Dalrymple, the Willard and Lillian Hackerman Professor of Civil Engineering and department chair. Schafer “takes a more collaborative approach—to get information out and in use, rather than to keep it private or market it,” Dalrymple adds.
Design Challenges of Cold-Formed Steel
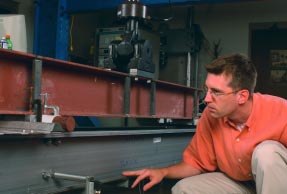
Schafer’s research is broadly based on civil structural engineering design, especially those designs that employ cold-formed steel. Unlike hot-rolled steel structures (such as I-beams) that are actually rolled into shape with hot molten metal, cold-formed steel is made from 1 millimeter-thin sheets that are literally cold-bent into such shapes as supporting beams and columns.
Cold-formed steel has replaced timber as the major framing and support material for thin-walled structures. They help keep costs down because they minimize the use of materials. Thin-wall structures “are everywhere today,” according to Schafer. They range from industrial and residential low- and mid-rise buildings to ship hulls, aircraft skins, and buried structures such as culverts and tanks. In every case, cold-formed steel plays a key role in thin-wall construction, as supports for walls, roofs, and floors. That, Schafer says, is where critical design challenges arise.
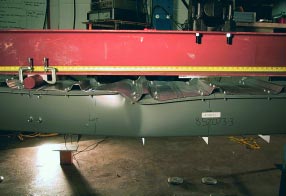
“The overriding characteristic of cold-formed steel—its thinness— is also the direct cause of its primary failure mode, which is buckling,” Schafer notes. “It’s unavoidable; that’s how they fail.” As an example, he demonstrates by pressing down on a straw held end-to-end between two fingers. The more push that is applied, the more the straw seeks to shorten itself in the same direction. Ultimately, the straw is unable to bear the load and collapses, buckling outward.
“And that’s where I come in,” he says, smiling. While finishing up his PhD in structural engineering at Cornell University in 1997, Schafer began to look for a means by which thin-walled structures could be designed more efficiently. “Traditionally, in civil structures, such design has been done using long and laborious hand formulas—formulas that have quite a few (though conservative) approximations in them,” he says. To provide more exact calculations on what variables cause a structural member to buckle, Schafer developed a software program called CUFSM (Cornell University Finite Strip Method). By publishing it on the web as open-source freeware, he enables other developers to make updates and improvements to the code. “My desire was to make this software available free to any engineer who wanted to use it as a tool in design,” Schafer says. “That’s the reason that it’s always been open-source.”
Based on the user’s input of building materials and structural features, CUFSM outlines every possible way that the specified thin-walled structure might buckle, and at what load. In turn, those data provide precise input into a structure’s design development, which is of enormous potential value to structural engineers and builders.
Coding with International Input
In the six years since its initial release, Schafer’s software has gone through a continuous series of updates and refinements, due to its growing collaborative use by hundreds of researchers in more than 14 countries. “Just this morning, a guy in Sweden whom I’ve never met nicely improved a small bit of code that I’ll incorporate, while adding his name to the list of developers,” Schafer notes. “This is something that happens a lot in computer science but is now just starting in civil engineering.”
Dalrymple views this process as productive for all concerned. “This collaborative approach accelerates research and eliminates duplication,” he says. “Why should another researcher somewhere else have to reinvent the wheel? When Ben publishes his code, it’s much easier for other researchers to get up to speed and help with the development of it. Since he’s helped them, they also want to contribute to making the code better.”
At the same time, Schafer is also developing a new design methodology, called the Direct Strength Method, which engineers can use in tandem with CUFSM. “This design method can take the input from CUFSM and apply it to a specific methodology to provide you with a reliable design,” Schafer says. “As an approved method that engineers in cold-formed steel could use for the design of their structures, that’s a pretty big deal.” According to the civil engineer, this methodology, currently under review by the American Iron and Steel Institute, could be adopted for use very soon.
While Schafer admits that “it’s a long process to get civil engineers to change the way they do things,” he is optimistic that his collaborative approach will help accelerate that process. “For me, the sharing is where the rewards come,” he notes. “I learn more by having people nose around in my work than I ever would by nosing around their work. It’s great—it brings innovation right to my doorstep.”
For tutorials and the free download of Benjamin W. Schafer’s CUFSM software, go to www.ce.jhu.edu/bschafer