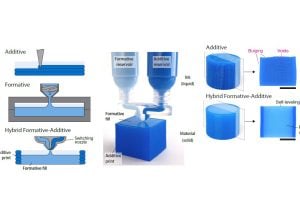
Researchers from the Department of Civil and Systems Engineering (CaSE) in the Whiting School of Engineering have introduced a method that tackles one of 3D printing’s biggest challenges: the tradeoff between speed and quality. The method, called Hybrid Formative-Additive Manufacturing, or HyFAM, combines the precision of additive manufacturing with the efficiency of formative techniques like casting and molding.
“Instead of viewing additive and formative manufacturing as competing methods, we had the idea to marry the two,” said Jochen Mueller, CaSE assistant professor and principal study author. “By combining the benefits of each, we created a new production method that also overcomes some of their major drawbacks.”
The study appears in Advanced Materials.
Additive manufacturing—or 3D printing—offers customization and material versatility, though it is often slow and prone to defects caused by limitations of the circular nozzles used. In contrast, formative manufacturing methods—such as molding or casting—produce high-quality parts quickly, but require complex tooling and offer less design flexibility.
HyFAM bridges the gap between the two manufacturing methods. It speeds up production by using a casting-like process to quickly fill bulk sections where fine detail isn’t needed, while relying on traditional 3D printing for high precision areas, such as outer surfaces and intricate features. This hybrid approach avoids the inefficiency of printing every part voxel-by-voxel when only a small portion of the object requires high resolution or more detailed features.
“Additive manufacturing offers significant detail, but when you use a small nozzle to achieve it, the entire process slows down,” said team member Nathan Brown, a doctoral candidate and first author of the paper. “This becomes a real hinderance in parts with large internal features and widely-varying feature sizes.”
According to Mueller, when compared to conventional 3D printing, HyFAM can be up to 10 to 20 times faster for objects with significant cast-like fill and roughly twice as fast for detail-heavy prints.
To demonstrate HyFAM’s versatility, Mueller and Brown printed objects using a wide range of materials suitable for material extrusion. These included silicone, ceramics, metals, epoxy, cement, clay, and even chocolate. The process required precise control of how the material flowed and how thick it was to ensure even filling. It also relied on choosing materials that would behave similarly once solid, to avoid issues like shrinking and warping.
The infill stage can span one, several, or all printed layers, eliminating the need to build layer-by-layer as traditional 3D printing does. It also helps bond 3D printed sections together uniformly, avoiding gaps and other common flaws.
The researchers say their method is particularly effective for mass customization scenarios, where objects have both detailed and non-detailed sections.
“HyFAM is less advantageous for highly intricate, uniform objects, but its strengths in combining speed, material flexibility, and design complexity make it a promising solution for a wide variety of industries, from construction to soft robotics,” said Mueller.
Mueller and Brown plan to expand HyFAM’s capabilities by experimenting with different materials and incorporating materials with different mechanical properties to broaden potential applications.