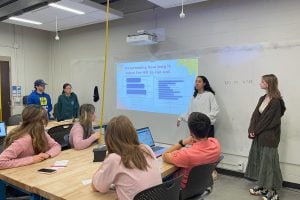
Few things are more disappointing than walking into an ice cream shop, craving your favorite flavor, only to find out it’s sold out. First- and second-year students in the Department of Civil and Systems Engineering (CaSE) put their systems engineering knowledge into practice to solve this very real disappointment. As part of a class project, students were tasked with addressing real-world inventory challenges for Taharka Brothers Ice Cream in Baltimore, which serves small-batch ice cream flavors in scoop shops and restaurants throughout the city and the surrounding area. As part of their course Civilization Engineered: Data Driven Solutions for Communities, students developed solutions to optimize the ice cream inventory management process and enhance delivery scheduling at one of Taharka Brothers’ scoop shops to ensure flavors were always in stock.
The project was designed by Melissa Tilashalski—CaSE lecturer and director of undergraduate studies for systems engineering—in collaboration with junior systems engineering major Diran Jimenez. Using data provided by Taharka Brothers, which included the number of ice cream tubs sold at the company’s Cross Street Market shop from January to September 2024, students were asked to solve key inventory issues such as communication of low inventory, stock shortages, and limited cold storage capacity—only two tubs per flavor.
Divided into teams of four to five students, each group analyzed the existing data from Taharka Brothers with the aim of developing alternative inventory management systems and a more efficient delivery schedule using systems engineering models taught in their course with Tilashalski. One critical constraint was that the proposed system needed to be simple and eliminate the need for a computer. Each team had a goal of developing an efficient and economical inventory and delivery system that would ensure customer satisfaction by maintaining consistent availability of Taharka Brothers’ most popular flavors.
Midway through the spring semester, students presented their analyses and proposed solutions during class. One team, including Ryan Lindsey, Timothy “Timbo” Liang, Eddie Zhu, Justin Kim, and Andrew Myers, analyzed the average number of days between restocking a flavor to develop a new delivery schedule. The resulting and delivery plan was projected to reduce costs by 44% over nine months, saving approximately $240. Another group, consisting of Quan Do, Lacey Downey, Carolyn Johnson, Diego McHenry, and Briana Roberts, proposed a modified delivery schedule that eliminated least popular flavors during peak summer months to allow for greater quantities of high-demand flavors.
To address restocking communication challenges, another team that included Joann Li, Emma Dionne, Sarah Fleming, and Rosario Hernandez, proposed a two-sided, color-coded disc system. Green indicates that a backup tub is available, while red signifies that the second tub is in use, prompting employees to add that flavor to the next restocking delivery.
By integrating systems engineering principles into inventory management and delivery logistics for Taharka Brothers, students could see the real-world impact to the scoop shop’s operational efficiency. Through analysis of existing data and the development of data-driven solutions that can be applied to everyday business challenges, the students were able to develop valuable hands-on experience in their field.