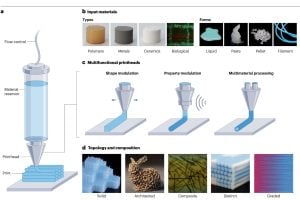
Additive manufacturing, or 3D printing, has evolved far beyond its early days as a niche industrial process, giving rise to applications like architected metamaterials with tunable mechanical and optical properties, functional tissues derived from living cells, and soft robotics with integrated actuation and sensing. Despite these advances, 3D printing methods still face significant constraints when it comes to material diversity.
“3D printing techniques are often restricted to specific materials like UV-curable polymers, thermoplastics, or particular alloys,” said Jochen Mueller, an assistant professor in the Whiting School of Engineering’s Department of Civil and Systems Engineering at Johns Hopkins University. “But there is one major exception—Material Extrusion 3D printing. Material Extrusion currently offers the broadest range of materials options, from polymers to metals to ceramics, and can even combine them in a single print. This is made possible by advances in printhead technology, which are the most critical component of multimaterial extrusion 3D printing.”
In a new review published this month in Nature Reviews Materials, Mueller and co-authors, doctoral candidates Nathan Brown and Daniel Ames, offer a comprehensive overview of the rapid evolution of this field. They also present their perspective on the future of 3D printing, highlighting the emergent role of advanced printhead technologies in expanding material and design possibilities.