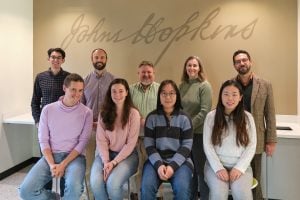
Supported by a $2 million grant from the National Science Foundation’s Designing Materials to Revolutionize and Engineer our Future (DMREF) initiative, a team of researchers at Johns Hopkins, Washington University in St. Louis, and the University of Wisconsin—Madison aim to adapt metallic glass for use in additive manufacturing. Comprising a mix of metals which add strength and flexibility to objects like golf clubs and surgical instruments, metallic glass is typically formed into products through a process called mold casting. However, the quick cooling required to solidify a metal into a glass makes it difficult to create thick parts that don’t have crystals, which can cause microscopic weaknesses in the material.
“We believe that metallic glasses might cooperate well with additive manufacturing since they do not exhibit crystallization that can give rise to weaknesses. What we learn from controlling the manufacturing process could allow for stronger metallic glass objects,” said Hopkins team leader Michael Falk, professor of materials science and engineering at the Whiting School of Engineering.
Commonly known as 3D printing, additive manufacturing may be the future of metal parts manufacturing, Falk says, pointing out that the process of building layer by layer could render traditional mold casting—which requires a lot of energy and investment in a pre-determined design—obsolete. Additive manufacturing holds the potential for a more environmentally sustainable approach to production.
“It can be more energy efficient than other processing methods because you’re delivering the heat only where you need it,” says Falk. “It could result in more customizable and sustainable ways of making things.”
Currently, the use of plastics is commonplace in 3D printing, and Falk hopes the same will soon be true for metallic glasses. The team is focused on solving one issue: The crystal deficiencies that form when the material cools and is reheated on subsequent passes of the laser, which presents an obstacle to the additive manufacturing of these materials.
“The problem with glasses is that if they aren’t carefully processed, they can crystallize. It’s not so easy to make a metal into a glass,” he says.
These weaknesses provoke anisotropies: the crystals occurring within the materials, causing the microstructure to face different directions. These defects form when glassy metals cool too slowly or are repeatedly heated and cooled. To mitigate deterioration, metallic glass must quickly cool and harden while maintaining a liquid-like arrangement at the atomic level.
Falk and the team are confident that additive manufacturing has the potential to eliminate crystal anisotropies because both 3D printing and metallic glasses favor rapid cooling.
“With additive manufacturing, you’re using a laser, you’re putting down some powder, while shooting the powdered surface with a laser. Consequently, you’re cooling the material very quickly,” says Falk. “That’s a natural way to make metallic glasses because it’s easier to create glass if you’re cooling very quickly. So, metallic glasses are good for additive manufacturing, and additive manufacturing is good for metallic glasses,” he says.
To develop this technology, the researchers are conducting cyclical experiments spanning 4 years, with one part of each effort informing another. They aim to develop processing methods that will reliably produce strong metallic glass parts.
“The grant is focused on a collaboration between people who are doing the actual additive manufacturing and people who are doing the computer modeling – trying to understand what’s happening from a physics and material science perspective so we can control what we are manufacturing,” says Falk.
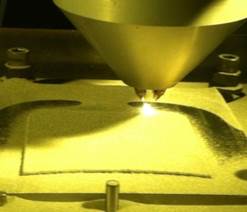
The additive manufacturing process, a laser melting powder onto a surface. Photo by Katharine Flores, Washington University in St. Louis.
The scientists will start by depositing powders of copper and zirconium on a surface and melting them with a laser, mimicking additive manufacturing. Then, they will characterize and analyze how the atomic structure of the samples changes under heating as a starting point for computer simulations. Those simulations will predict the behavior of the metallic glass parts under various conditions, including temperature changes, brightness of the laser, and the speed of powder deposition. The simulation-based models will be integrated into prediction codes, enabling researchers to assess the conduct of the actual materials versus the predicted outcome.
“We will use that information to strengthen them for future experiments. By repeating the process with different processing conditions, we intend to discover method of layering metallic glasses that does not cause crystallization and anticipates what the material will do once the part is created,” Falk says.
Falk’s part in the process is to interpret the materials science and physics behind the computer simulations and code the findings into equations. He uses models to connect the complicated details— the exact combination of elements, methods to characterize the glass, and so on—to the simulations.
“I’m a theoretical physicist at heart,” says Falk. “Trying to understand how a material behaves and write that down as equations is like magic to me.”
The team hopes that what they learn will contribute to the overall expansion of additive manufacturing and can be used for applications from 3D printing everything from car engines to airplane wings. Although some applications for 3D printing seem far-fetched, Falk claims that this research may be one step closer to making them a reality.
“Additive manufacturing is a totally different way of producing stuff,” says Falk. “We have all these techniques we use to make all things in our built environment; from consumer goods to airplanes, houses, and more. I think the way we make things is going to change radically over the next few decades.”