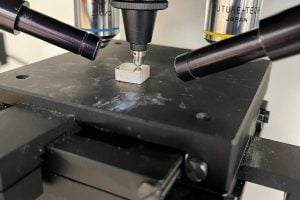
Biodegradable magnesium alloy implants promise to revolutionize bone repair, naturally disintegrating as broken bones heal and eliminating the need for removal surgeries. However, their too-rapid breakdown in the body has hindered their effectiveness—until now.
A team of Hopkins researchers discovered a new way to create magnesium alloys that can endure the harsh conditions inside the human body, giving broken bones time to heal before they disintegrate. Led by Tim Weihs, a professor of materials science and engineering at the Whiting School of Engineering, the team used a rapid testing and processing method combined with machine learning to identify the ideal microstructure for alloys to thrive within the human body. Their findings were published in the Journal of Magnesium and Alloys.
“To slow the alloy’s breakdown in the body, we would previously change its composition – substituting zinc or calcium with a different metal,” said PhD student and team member Sreenivas Raguraman. “However, in this research, we discovered that altering an alloy’s composition isn’t necessary to improve its strength and inhibit degradation. Instead, we can finetune the manufacturing process to achieve better results. The innovation is not in the steps themselves, but rather in the unique way they are combined that strengthens the alloy.”
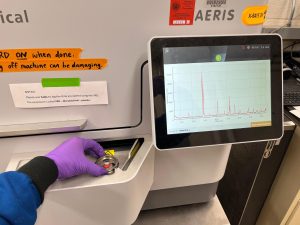
The alloy sample loaded into x-ray diffraction, which analyzes its microstructure.
The team studied the structure and properties of the material after subjecting it to an 11-step process. First, they applied a method to reshape the material and improve its strength and then subjected it to heat. The team then used X-ray diffraction and microscopy to visualize the structure of the materials. Next, they tested the material’s strength by pressing a tiny tool to its surface to measure how much force it could withstand and then placed the alloy in an incubator that mimics conditions within the human body. Finally, the team used a machine learning technique called LASSO regression to identify which structure had the greatest impact on material stability and durability.
The team found that the material’s strength and resistance to corrosion or deterioration improved – showing that researchers can refine the material using this new process. They also discovered that a single minute of heat treatment at 450 degrees Celsius can dramatically enhance the alloy’s durability.
The researchers say that these promising results, along with faster processing, make this material ideal for use in biodegradable implants.
“Moving forward, we want to develop a numerical model to predict strength and corrosion rate as we adjust processing steps,” said Raguraman. “The more information we feed into the machine learning tool, the more precisely we can predict the materials’ behavior. This would be a huge step towards developing customizable biodegradable implants.”
The study team included Paulette Clancy, Edward J. Schaefer Professor in Engineering in the Whiting School of Engineering’s Department of Chemical and Biomolecular Engineering and postdoctoral researcher Maitreyee Sharma. Adam Griebel at Fort Wayne Metals worked with the team on experimentation.
“We hope to continue this very productive collaboration and identify other processing routes for multiple magnesium alloys in the future,” says Weihs.