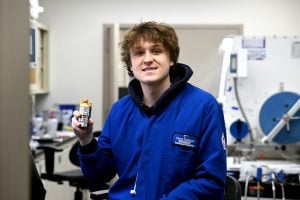
Senior materials science and engineering student Liam McMullin is designing a sturdier battery component for solid-state lithium batteries that could help electric vehicles and cell phones run longer between charges. His project focuses on improving the cathode—a critical component inside these advanced batteries—by investigating how different sizes and properties of the materials that store and transport lithium and electrolytes affect the battery’s overall performance. He presented his findings on April 29 at the Whiting School of Engineering’s Design Day, an annual event showcasing students’ innovation and ability to translate theoretical knowledge into real-world solutions.
“Typical lithium batteries use a liquid electrolyte to move ions between the anode and cathode. Solid-state batteries use a solid material instead, which can cause the active material to crack and lose contact with the electrolyte, significantly limiting battery life,” says McMullin. “I’m designing a new cathode to reduce this mechanical damage by optimizing the active material’s particle size and the electrolytes’ mechanical properties.”
McMullin is studying the internal forces that stress the battery’s solid material, revealing how the mechanical forces contribute to degradation. In the lab, he used ball milling —a process that grinds down material with a ball-filled rotating cylinder—along with heat treatments to create two halide electrolytes, materials commonly used in solid-state batteries, so he could experiment with them.
After ball milling, McMullin conducted ultrasonic velocity measurements to characterize the material’s mechanical properties. He used a device called an ultrasonic transceiver which sends an acoustic wave through the material and measures how quickly it returns—information that reveals information about the material’s stiffness.
“These measurements give us an idea of how much stress this material will generate in the cathode, so we can predict how much mechanical degradation will occur inside the battery,” says McMullin.
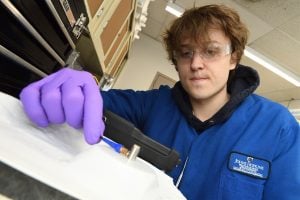
McMullin testing the material for use in a solid-state battery.
Then, he used dynamic light scattering and laser diffraction to determine the particles in the active material.
“Knowing the particle sizes and their distribution helps to understand and control the microstructure of the cathode. This also allows us to optimize the transport of lithium ions in the cathode, so we can get higher performing batteries” he says.
After the material was prepared, it was placed in cathodes within a battery cell to see which mixtures of material performed best. McMullin mixed the active material with an electrolyte, an electronic conductor, a polymer binder, and a solvent to create the composite cathode. He assembled cathodes with different ratios of materials and placed them in two batteries to see whether a stiffer electrolyte leads to more mechanical degradation.
“We can measure the force changes during battery operation and estimate the stress the materials within the battery are experiencing, then correlate this to the mechanical properties of the electrolyte and, possibly, the particle size of the active material in the cathode,” he says. “If the stress is higher in the electrode, it’s more likely for the active material to degrade and crack. By testing these cells, I can design a cathode that uses the materials that perform the best in the batteries I create.”
McMullin completed his research under the guidance of Regina García-Méndez, assistant professor of materials science and engineering and core faculty of the Ralph O’Connor Sustainable Energy Institute (ROSEI).