
Inside the historic Stieff Silver Building, Johns Hopkins has built the world’s top facility for studying the atomic structures of materials. Researchers across the Whiting School are using it to reshape fields from energy to oncology.
The alligator gar is not an attractive fish. It boasts a long, toothy snout that looks like a cross between a duck’s bill and an alligator’s grin, by which it earned its name. It can grow to well over six feet and weigh upward of 300 pounds. The alligator gar is a formidable predator, too, but being an apex predator does not mean it lacks natural enemies. And that notion raises the question of why such an ungainly species has survived, virtually unchanged, for nearly 200 million years.
That endurance, say evolutionary biologists, is likely due to the alligator gar’s remarkable spade-like scales. They are just plain tough. It was that toughness that brought the Army Corps of Engineers to Ken Livi, a research scientist and director of operations at Johns Hopkins’ Materials Characterization and Processing (MCP) facility.
The Corps came calling, hoping he might use the array of world-class imaging tools at Johns Hopkins to reverse engineer why those gar scales are so durable and to possibly turn that knowledge into better armor and shielding, like those that protect spacecraft on reentry.
TOOLS OF THE TRADE
The tools of Livi’s world—electron microscopes, spectroscopy, X-ray computed tomography, and others—would allow his team to peer into the very atomic structure of the alligator gar’s scales. In all, Livi used no fewer than eight imaging and analysis technologies to examine the scales.
In the end, the team confirmed that the scales comprise an outer layer of ganoine, a hard material akin to tooth enamel, sitting atop a porous-yet-flexible bone-like material. Critically, Livi and team discovered that the two layers are not fused or otherwise glued together, but bound by “rasps” of hydroxyapatite (HAp) extending from the underside of the enamel into the bony structure below. What’s more, those rasps are angled toward the outer edge of the scale to create anchoring points, like tent stakes, locking them in place and preventing the material from fracturing into layers, or delaminating, and distributing load when compressed by, say, a predator’s bite.
“What makes this material so fascinating is that every part of this simple scale is exquisitely engineered for a purpose,” Livi explains. “The rasps angle in and keep the enamel from popping out. Even the arrangement of collagen changes depending upon its location. We couldn’t have learned any of this without tools like those at the MCP facility.”
NOT YOUR MOM’S MATERIALS CENTER
Such is precisely why, not long after Livi’s research was published in 2016, Johns Hopkins began to invest aggressively in the Materials Characterization and Processing facility, putting more than $25 million into this state-of-the-art lab, classroom, and office space. The MCP today boasts a collection of processing and characterization equipment that is, in its entirety, is considered unmatched in the world.
“This may seem like your ‘mom’s materials center,’ but it’s not at all,” says Mitra Taheri, a professor of materials science and engineering at the Whiting School and director of the Materials Characterization and Processing facility.
“It’s really something built for the next several decades of science,” says Taheri, who also heads the Whiting School’s Dynamic Characterization Group and serves as a Faculty Fellow of the Hopkins Extreme Materials Institute. “The MCP is a development lab where we’re working with microscope and processing manufacturers to remake these tools with embedded artificial intelligence and computing toolsets to be ‘thinking machines’ for processing autonomy. We’re both synthesizing new materials and helping create new tools to produce [those materials].”
The facility is overseen by the School of Engineering, but available to any researchers at Johns Hopkins as well as corporate and government clients eager to lease time on its cutting-edge machinery. All have a vested interest in peering deeper into materials than ever before and creating bespoke materials for next-generation applications. The MCP makes that possible as never before.
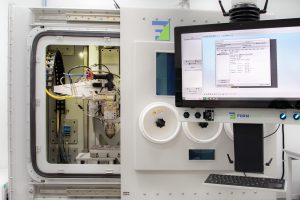
A NEW KIND OF 3D PRINTER
Stepping into the 13,000-square-foot Materials Characterization and Processing facility is like stepping into the structure of matter itself. The progressively more powerful microscopes and other tools are arranged along a single corridor. Each successive room plays host to equipment that, incrementally, peers deeper into and controls the structure of new-age materials at the atomic scale—from the micro-computed tomography machines at the front of the hall to the gleaming new scanning transmission electron microscopes at the far end.
One of the first rooms along the way is home to the Directed Energy Deposition machine, a material-creation tool that literally builds bespoke alloys layer by layer. It hosts a ring of vials that can each be filled with different elements that can then be drawn in, little by little, and melted into specific structures by a laser.
“It’s a new kind of 3D printer,” Taheri says. “The laser ‘writes’ a new alloy layer by layer but as we’re feeding it the raw materials, we can make changes atom by atom. It’s like baking as you pour in the batter. It gives us unprecedented control over materials design.”
Taheri leads a center-of-excellence partnership with Formalloy, the maker of the DED, to move beyond iterative, additive manufacturing and use ultrafast EDGE computational power and AI/machine learning control for real-time feedback and control of the synthesis process.
Surprisingly, perfection is not the objective, for it is the imperfections, Taheri explains, that determine a material’s valuable physical properties, like tensile strength, energy storage, and electromagnetic efficiency. Sometimes those imperfections are the result of “happy accidents” that lead to breakthrough materials. More often, they are the result of careful research and supremely controllable synthesis.
Increasingly, researchers are designing materials on the computer, then coming to the MCP facility to build their creations, explaining the “P” in the MCP moniker— “processing.” Taheri, for instance, is using the DED to design next-generation electric vehicle devices and motors under an ARPA-E (Advanced Research Projects Agency- Energy) program for energy-efficient magnets. Similarly, as part of a different global, multi-university team, she is using the DED to develop high-temperature alloys that resist corrosion and oxidation for use in demanding aerospace and marine environments.
The facility also plays host to a multidisciplinary group of Whiting faculty that is contributing to AI-enabled toolsets for bioprocessing, chemical and structural characterization, in operando control, and more.
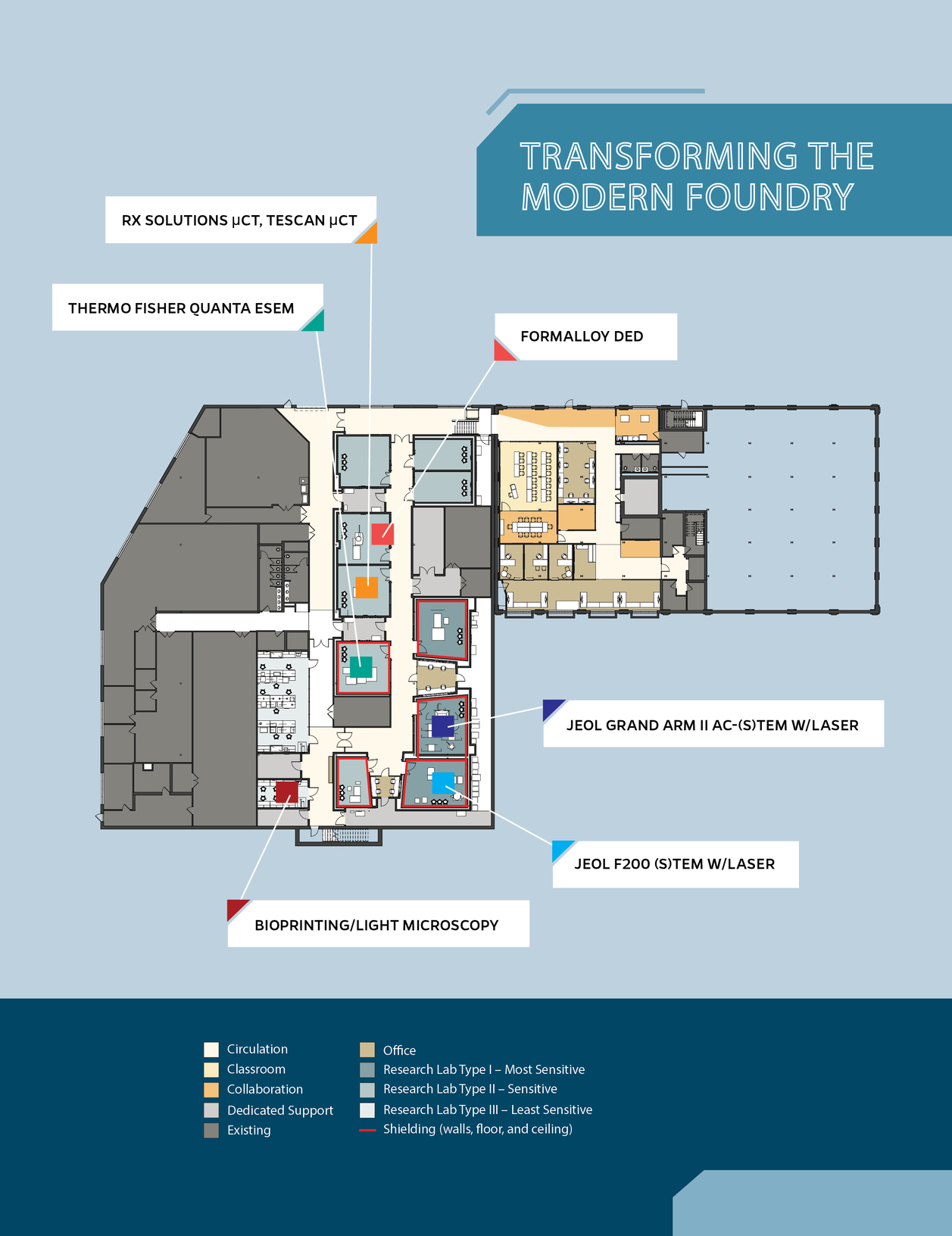
“Many of the materials we study are built from the atom up. We use these smart machines to build parts and materials right the first time, every time. The hardest part is often getting the raw materials,” Taheri says, noting that most nickel is mined in war-torn Ukraine. “We have probably $100,000 in powdered nickel in that vial right there.”
Kevin Hemker, the Alonzo B. Decker Chair and professor of mechanical engineering who directs the Johns Hopkins Center for Additive Manufacturing and Architected Materials (JAM2), knows this territory well. As the name of the center implies, the researchers at JAM2 are creating architected materials for highly specific, highly demanding applications like space travel, jet engines, new-age armor, and the like.
“In these cases, the question often comes down to how additive manufacturing affects the material at the microstructural and atomic scales,” Hemker explains. His research, conducted in collaboration with Jamie Guest, head of the Department of Civil and Systems Engineering, often involves architecting a material on a computer, creating it via DED or laser powder bed fusion (L-PBF), measuring its properties, and, finally, looking into the material, often to the atomic scale, to understand why this particular instantiation of the material has such highly sought-after properties. In his work, in JAM2 and at the JHU Applied Physics Laboratory, where he is a senior member of the technical staff, Hemker and his students often take advantage of the MCP’s broad range of equipment.
“We use scanning electron microscopes a lot because backscatter mode allows you to see the individual crystallites and map their orientation within the material,” he says. “Understanding crystallographic texture explains a lot about why the material behaves the way it does.”
Often, his work involves elucidating a material’s unusual properties and then, and only then, going to MCP to figure out how and why the material behaves the way it does. One recent example, a collaboration with researchers at APL, involved the additive manufacturing of metal-matrix composites.
“The APL researchers discovered that the additively manufactured metal-matrix composite exhibited both enhanced mechanical properties and environmental resistance,” Hemker explained, “and we were able to show them how the atoms rearranged themselves during the additive processing, which helped explain why the material has the properties it does.”
IN EXTREMIS
At the next stop, a team of researchers huddles around a computer terminal next to a gray box the size of a large armoire. On the computer screen is a 3D image of a round mass that that looks a bit like a ball of falafel. It is, in reality, a digital image of cemented sand developed for the Hopkins Extreme Materials Institute.
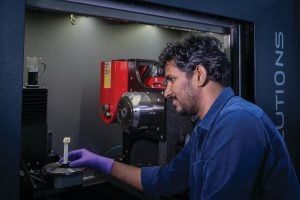
The lead researcher at the computer this day is Ryan Hurley, an associate professor of mechanical engineering and Faculty Fellow at HEMI. The machine in the gray box is a micro-CT—microcomputed tomography— one of the key technologies Livi used to image the garfish scale. Micro-CT uses X-rays to create three-dimensional digital images of the material in question.
Nearby, Hurley’s real-world sample sits inside the micro-CT within a custom-built device that simulates an extreme environment. Hurley can dial up the pressure, tension, and other stresses while imaging his sample in three dimensions in real time, analyzing the points of failure using computer algorithms.
Such cemented sands can be found everywhere on the surface of the Earth and on planetary bodies throughout the solar system. The way that they respond to mechanical loading is critical for such disparate needs as constructing buildings or predicting the effect of an asteroid impact. Hurley takes what he learns at MCP back to the lab to fine-tune numerical models to accurately predict how the materials will behave in the real world.
“Micro-CT lets us look inside a 3D sample and actually see how it’s breaking down at the microstructural level,” Hurley says.
THE ‘ZERO’ ENVIRONMENT
The next room includes the first piece of equipment in the facility to resemble a traditional microscope, albeit at tabletop scale—an entire tabletop, that is. What would traditionally be an eyepiece plays host to a digital camera transmitting imagery to an observation room nearby. This is what is known as a focused ion beam-scanning electron microscope, a FIB-SEM. It operates on the same principle as a traditional light microscope, Taheri says, but employs a beam of ions to slice into a sample in ultrathin layers while a column of electrons illuminates each cross-section for high-resolution imaging.
Electron microscopes, like the transmission electron microscope (TEM) in the next room along the hall, have an electron beam that is far more sensitive than any light-based microscope, Taheri says, but are also much more “finicky.” With a TEM, the slightest vibration (a footstep or the slightest sound) can imperil results.
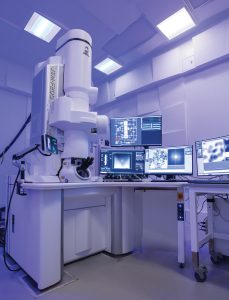
“We need a zero environment—no vibrations, no interference. With some of these more sensitive transmission electron microscopes, the samples are so small a single breath—‘huh,’ just like that—and it’s curtains,” Taheri says, making a slight puff for dramatic effect.
A key decision in creating a zero environment was Johns Hopkins’ choice to forego a new building and instead renovate the Stieff Silver Building at the southwest corner of campus. While the building’s legacy as a precious metal foundry provided a metaphorical hook—Taheri refers to the facility as “transforming the modern foundry”— something more was at play. The Stieff building rests directly on bedrock, an unmatched foundation for the MCP’s ultrasensitive machines.
All rooms are individually isolated to further dampen vibration. Inside, the rooms look more like recording studios than labs. The hospital-white walls are canted slightly so as not to meet at right angles, and each is peppered with odd-angled acoustic panels to further deaden sound. Many rooms are fitted with large cooling panels that hold temperatures within tight specifications to eliminate thermal expansion and contraction that can likewise imperil results. Last but certainly not least, the most sensitive electron microscopes are also prone to electromagnetic disruption and must be shrouded in room-within-a-room metal superstructures that jam interference.
LIVING ON THE EDGE
The full import of such meticulous dampening becomes apparent a minute later as Taheri walks out of the lab and down a door into the u-shaped hallway surrounding the FIB-SEM lab, where the ear is deluged by noise. It is the fever-pitch of fans and pumps straining to cool the computer equipment churning through the vast data the microscopes are spitting out.
These are next-generation EDGE computers. They are so fast that proximity to the source is a key factor in their performance. They are literally at the “edge” of the labs they serve. Taheri notes that some of the microscopes are capturing 20,000 high-resolution frames per second.
“This is an exciting capability and demands this type of next-generation computing as we are bringing in data so rapidly that we must develop new computing algorithms and devices to manage and process it all,” Taheri says. “Levering EDGE computing will get us closer to our vision of autonomous labs by allowing computers to make rapid decisions about an experiment as it’s happening.”
Likewise, the many terabytes of data flowing out each second means heat— a lot of heat. All that firepower must be cooled to function properly.
“You’re looking at the sausage-making machinery of the MCP,” Taheri shouts above the din of fans. Meanwhile, in the lab, just few feet away through the wall, people talk in whispers.
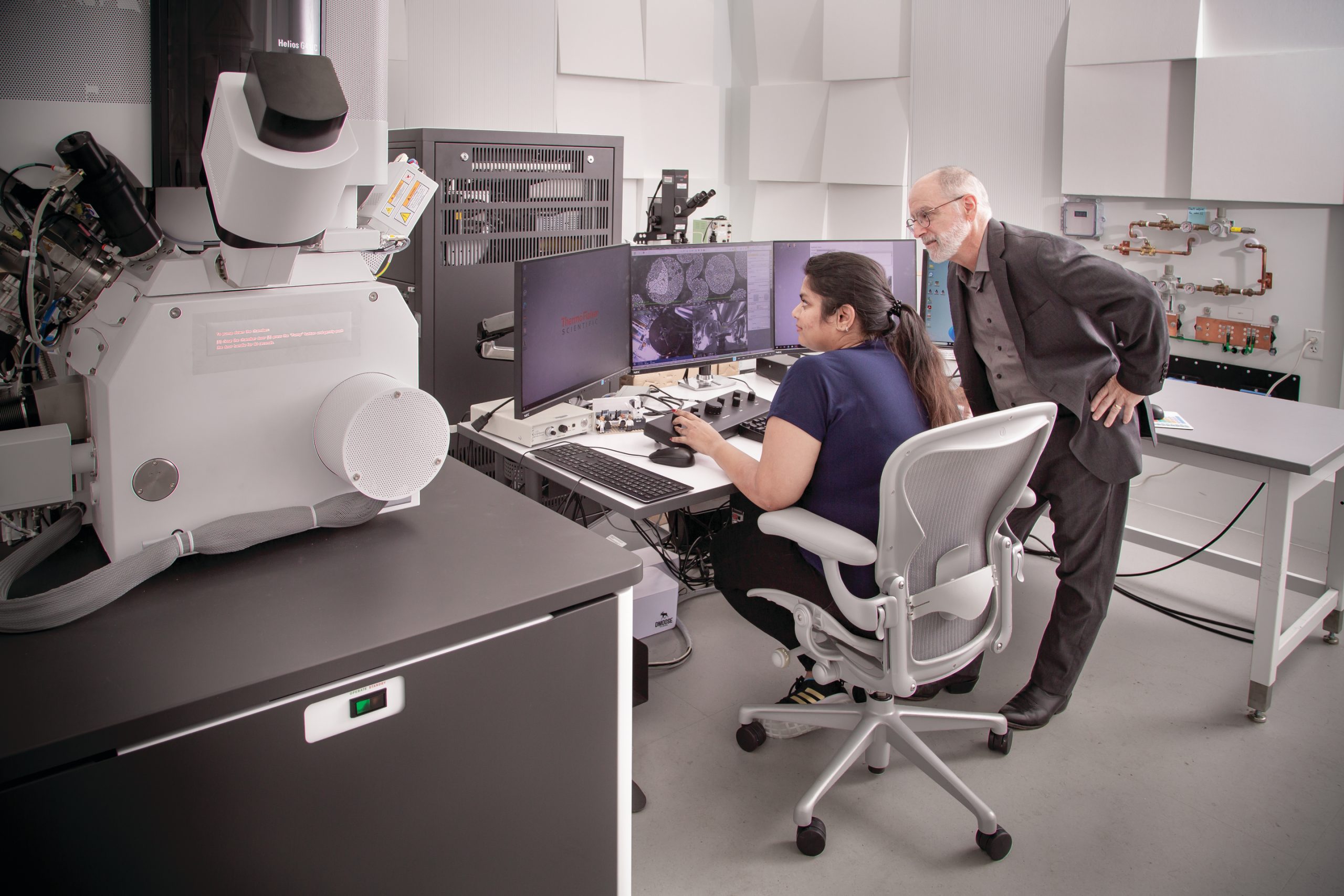
AN UNPRECEDENTED LEVEL
Next, Taheri leads to a room that contains the newest microscope at the MCP, the JEOL Grand ARM II (JEM-ARM300F2). It is currently the only one of its kind in the United States as it was acquired through a cost-sharing Center of Excellence partnership with the manufacturer Japanese Electron Optics Laboratory and its subsidiary, IDES. The ARM II acts not only as a tool for the community of users looking into interesting materials such as quantum, structural, biological systems, but also as a landscape for the development of intelligent microscopy and novel characterization techniques that are both smart and ultrafast. The ARM II’s detectors and systems allow researchers to see and understand materials beyond anything that came before.
“The ARM II boasts subatomic resolution,” Taheri says proudly. “This is a Lamborghini compared to the Camry I learned on in graduate school.”
The scale bar on images from the Grand ARM II are often less than half a nanometer—two-billionths of a meter. The microscope showcases the world’s best sensing and imaging tools, that see materials smaller than an atom and can watch them move at rates orders of magnitude less than a second.
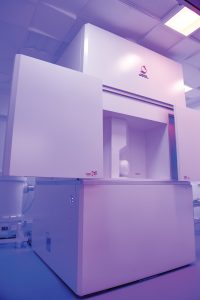
“This is the birthplace of new materials for computing, medicine, and more. This is the electron gun. And the specimen goes here,” she notes, pointing to the maze of tubes and wires that looks more like science fiction than a microscope of old.
The electron beam is fully controllable and able to make real-time decisions about how the beam is interacting with a sample to precisely calibrate energy and correct lens aberrations to achieve maximum resolution.
“We have a paper in transit with the first evidence of our ability to dose control to look at living tissues without harming them, which is a major advance in understanding biological systems that usually require being frozen in order to be imaged,” she says of the Grand ARM II’s exceptional control.
WALKING THE WALK
As we round the corner at the far end of the main hallway, the MCP facility has yet one more surprise in store. It is a bioprinter: a machine that can print synthetic biological tissues.
Yun Chen, an assistant professor of mechanical engineering and a researcher in the Institute for NanoBioTechnology, runs the Mechanical Engineering of Wet-materials Laboratory, the MEOW Lab. Her specialty is applying the mechanical analysis of intercellular forces to diagnose and treat conditions like cancer and heart disease.
It turns out that human cells adapt and adjust behaviors to the rigidity of their surroundings. Cancer cells will even respond differently to chemotherapies depending on the stiffness of their environment. Therefore, it requires different types of drugs and often varying dosages to kill cancer cells invading soft brain tissue versus hard bone. To more effectively screen new drugs and dosages, Chen employs the MCP’s bioprinter to fabricate synthetic tissues that have softness comparable to that of the targeted human tissue.
“The bioprinter in the MCP is capable of tuning the softness of the printed synthetic tissues to mimic any type of human tissue—brain, muscle, or bone,” Chen explains.
But cancer is not Chen’s only target. The bioprinter can print cardiac tissues that beat just like a real human heart. Chen’s group has published three highly cited papers demonstrating the potential of bioprinted cardiac tissues.
Already, Chen notes, “bioprinted cardiac cells can even be implanted into the damaged tissues of patients suffering heart failure.”
The key for both cancer and heart disease is to get the cellular composition and the rigidity of the fabricated tissue as close to the human tissue as possible. Empowered with a bioprinter that can tune the mechanical properties of fabricated tissues to those of real tissues, Chen is now turning her sights on clinical research and treatment strategies to diseases beyond cancer and heart disease.
“The takeaway from all this is that life is as much a mechanical process as a biochemical process. When diseases occur, biomechanics are often at play,” Chen says. “We can use that knowledge to understand and approach diseases in new ways. The MCP’s bioprinter plays a key role in helping us do that.”
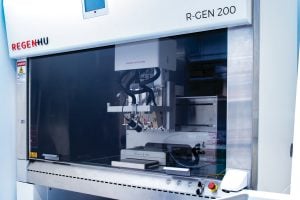
therapies.
THE BIG PICTURE
Tour complete, Taheri pauses a moment amid the handsome exposed brick of the Stieff foundry to consider all that is within its walls. With such a slate of impressive machinery—her “kids” as she calls them—Taheri says the next natural step for the MCP facility is something she calls “collaborative autonomy.”
“We want the ‘kids’ to play nicely together. We want these incredible, individual machines to think collaboratively, to move from automation to autonomy. The MCP is a large-scale effort to move Hopkins into the next great era of materials science and artificial intelligence,” Taheri says, pivoting back toward her office.