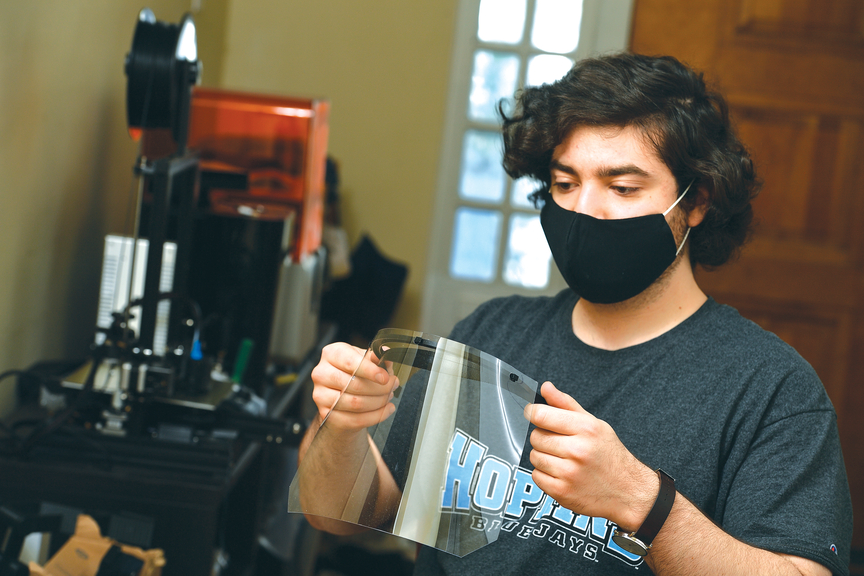
Late last spring, Chris Shallal juggled his preparation for final exams with a multicampus effort to create and provide durable, reusable face shields to health care workers at the Johns Hopkins Hospital.
To help fill the hospital’s urgent need for personal protective equipment due to the COVID-19 pandemic, the Johns Hopkins Consolidated Service Center recruited volunteers to assemble disposable foam face shields.
Shallal, a fourth-year biomedical engineering student, noted that the foam headbands used for these face shields do not hold up to prolonged wear and must be disposed of after a single use because the porous material could potentially trap hazardous particles. So, he and his engineering classmates at Health 3-D— a social venture co-founded by Shallal and classmate Kirby Leo ’20 that uses 3-D printing to improve health care products—submitted a proposal to the Johns Hopkins COVID-19 Research Response Program, detailing their plan to manufacture a more durable headband that would allow face shields to be worn multiple times. The student team was guided by biomedical engineering faculty mentors Elizabeth Logsdon and Warren Grayson.
The proposal was accepted, and the students were provided $10,000 to use toward printing materials. To make the headbands, the team uses extra-tough PETG filament, known for its strength and stability. It can be wiped down with basic cleaning agents, such as isopropanol, bleach, or ethanol, without affecting its durability.
Working with the Johns Hopkins COVID-19 Command Center, Shallal built a network of approximately 30 people and more than 55 3-D printers to create the reusable headbands using a printing design created by the Johns Hopkins University Applied Physics Laboratory.
Once printed, the headbands are dropped off at designated checkpoints and delivered to the Central Supply Chain warehouse, where a transparent shield and elastic band are attached to complete the new, more durable face shields, which are distributed into the hospital system.
“Setting up the network included onboarding new members and providing the appropriate 3-D printing feedback to ensure they could get the shields into production,” says Shallal.
He and his team are looking to increase production by recruiting more members and activating more printers. They are also considering other manufacturing methods, like vacuum forming or industrial casting and molding.