The Search for Tougher Materials
Advances in the science of computational modeling of materials and structures have made it possible not just to redesign materials traditionally used in armor and other defense applications, but to develop new ones.
That’s one of the goals of Somnath Ghosh, director of the Whiting School’s Computational Mechanics Research Laboratory and a leading member of the HEMI team. He develops state-of-the-art computer models to study the three-dimensional, multiscale effects of blast waves, including atom-by-atom responses of deformation, wear and tear, and impacts on structures made of crystalline and composite materials.
Ghosh, the Michael G. Callas Professor of Civil Engineering, leads the new Hopkins Center of Excellence on Integrated Material Modeling, a $3 million U.S. Air Force program to develop lightweight, durable alloys for aircraft parts and turbine engines—for use in everything from fighter aircraft to surveillance drones.
His contribution to efforts to make new armor and other defense-oriented structures includes work on tantalum, a hard, blue-gray metal, as well as epoxy-glass composites.
The goal is to systematically re-engineer materials that can provide protection against high impacts, such as a blast wave, with maximum efficiency. “You have to locally absorb the energy and disperse it as soon as possiblso you don’t have massive damage,” he says.
The research could have broad applications. Ghosh, for example, is working with Los Alamos National Laboratories and Army Research Laboratory on developing models for armor capable of shielding vehicles and buildings against high-impact situations, such as blast effects in a nuclear explosion.
“We want to know, what is the effect of an impact? How can we mitigate that? Is it even possible to do so?”
One key question, Ghosh says, is how candidate materials like tantalum fail when they reach the breaking point. The aim is to make sure that any new armor would respond in ways that would still protect whatever is behind it.
Ghosh points to modern automobiles as other candidate applications of his research. Today’s cars are designed to absorb and disperse the energy of a crash so the passenger compartment and people inside it are isolated from the shock. In a similar way, metal alloys can be designed to absorb and quickly disperse the energy from a projectile or a blast. “This energy absorption is a very important thing,” he says.
Another critical factor is weight. Heavy armor can slow people and vehicles down, making them more vulnerable to attack. One way to reduce the weight of armor is to use lighter materials.
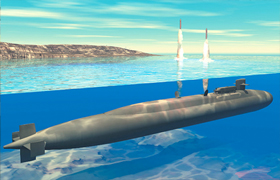
Tracking Submarines: Clues from Currents
Professor of Electrical and Computer Engineering Alex Kaplan’s research on ocean waves could lead to new forms of underwater sensing technology. more »
Another way to lighten the load is to use multiple functionality in future materials. Take the next generation of defense aircraft. A desirable way to reduce the weight and profile of a warplane, Ghosh says, would be to blend communications antennae and sensors into other structural aircraft components.
“Let’s say you have fuselage that behaves as an antenna, you don’t have to carry additional equipment,” he says.
The next generation of tougher, lighter, more durable materials will have an impact far beyond military applications, Ghosh says. “These new generations of computational tools, together with high-resolution imaging tools, give us an opportunity to look far deeper than people could do before,” he says. “Engineering is being coupled with fundamental sciences through the use of high performance computing and computational science and that is causing a revolution.”
Controlling the Cracks
Modern aircraft—both civilian and military— are made largely of aluminum alloys, which are prone to develop cracks that inexorably grow with repeated stress. And cracking can lead to catastrophic failures, like the one that hit Aloha Airlines Flight 243 in 1988, when the Boeing 737 lost part of its fuselage in flight.
James Spicer, PhD ’91, a professor of materials science, has conducted experimental studies for the Air Force on the internal structure of aluminum alloys. While he is not currently working with HEMI, Spicer’s research has generated the kind of data computer scientists need to build their models.
Specifically, he uses pulsed laser beams to set these parts vibrating like tuning forks, producing a kind of sonogram of their internal structure. The aim is to find hidden weaknesses.
If cracked aircraft parts undergo repeated stress and aren’t repaired in time, they can rip apart in midflight—a potentially disatrous turn of events.
Currently, he says, commercial airlines take aircraft out of service periodically to inspect them for cracks and metal fatigue. If they find rips or tears of sufficient size in the wrong places, they repair them. The military, with its specialized mission, takes a different tack. It simply swaps out old parts for new ones after a specified number of hours of service.
Spicer says neither approach is very efficient. The military’s practice of periodic replacement “is very costly, because you could be throwing away a perfectly good part,” he says.
The commercial airlines’ practice is not necessarily better, from the perspective of efficiency. “Taking an aircraft out of service at regularly scheduled intervals might not make sense either because the aircraft could be in perfectly good shape,” Spicer says.
Spicer’s work aimed at helping the Air Force develop ways to monitor the material “health” of aircraft parts, including the fan blades on jet engines, and based on that finding, predict when they are likely to fail.
Every time Spicer boards a commercial airliner, he says, he looks for cracks. All aircraft have some cracks, he says, though typically they aren’t a problem.
“The process of fatigue—where you have, let’s say, a crack in a material and you’re loading it and the crack grows very slowly—has been a problem that’s been around for a long time,” Spicer says.
But if cracked aircraft parts undergo repeated stress and aren’t repaired in time, they can rip apart in midflight—a potentially disastrous turn of events.
Spicer says one goal is to develop computer programs that, when fed data from a particular plane, can help spot cracked parts and predict how long they can safely be used.
Such a computerized safety test might help repair crews decide if further tests are needed, or just when the plane should be brought in again for a checkup. This could make maintenance cheaper and flying safer.
“A lot of people have worked on it to try to understand this better,” Spicer says. “And with the advent of the computational side of things in materials science and engineering, that’s provided new opportunities for doing a better job.”