For ships, tanks, and planes, multifunctional appliqués offer a more sophisticated way to avoid corrosion—and maybe detection.
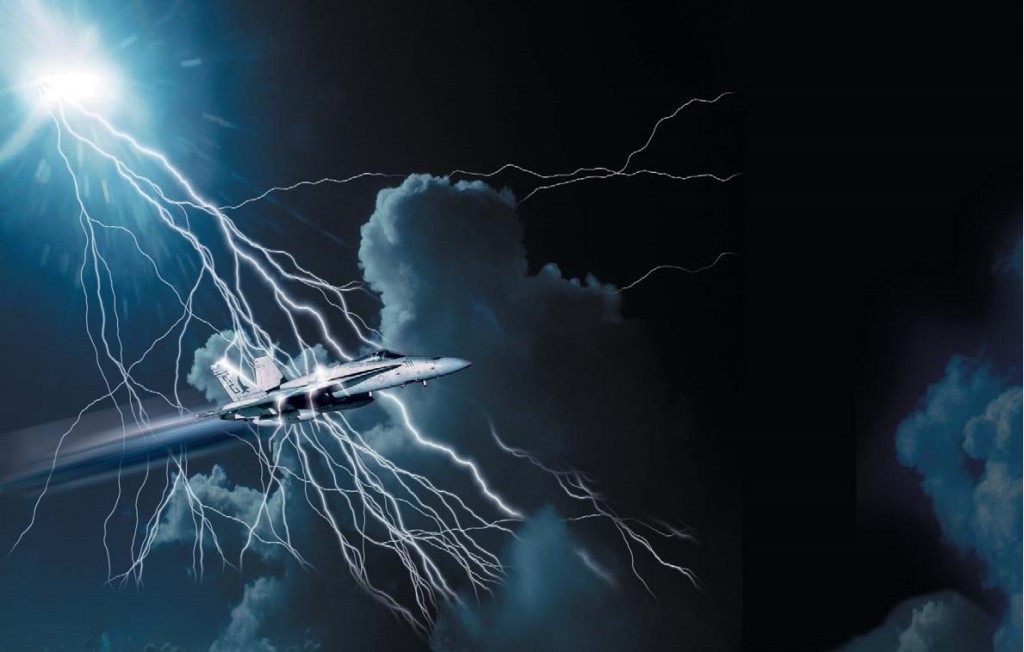
Some people see things as they are and ask, “Why?” John Brupbacher sees things as they could be and asks, “Why paint?”
That’s the question explored at the Whiting School’s Center for Multi-Functional Appliqué (CMFA). Appliqués are adhesive-backed plastics that resemble hi-tech wallpaper. Brupbacher is CMFA’s director and principal research engineer in the Department of Chemical and Biomolecular Engineering. He and his colleagues are examining how these appliqués may one day roll past paint as the coating of choice for military and other equipment in need of industrial-strength corrosion protection.
Metal exposed to such harsh elements as salt water, sand, sun, rain, and extremes in humidity and temperature demands constant maintenance, and that’s expensive. “The Department of Defense (DoD) has recognized that beating corrosion in the military is costing $10 to 20 billion a year,” says Brupbacher. There are environmental hazards related to stripping, sandblasting, and repainting tanks, HUMVEEs, airplanes, and ships. Then stir in the other factors impacting vehicles and equipment: the need for rapid camouflage changes to accommodate redeployment to different locales, the constant struggle to minimize electronic detection, and the desire to reduce surface friction of a ship’s hull or a plane’s wing. No wonder military planners are actively seeking tougher materials to preserve their materiel. “They have been looking for a better solution,” says Brupbacher. “One thing that is getting attention is appliqué.” Brupbacher and colleagues presented their work on appliqués last November at the military’s 2003 Tri-Service Corrosion Conference, which has been held biannually since 1967.
The advantages of a multifunctional appliqué are many, according to Brupbacher, as are the disadvantages of continuing to paint. “With paint, you have understood issues,” he says. While there are now solvent-free, lead-free, one-coat, and water-based paints, it’s still a medium with many limitations. Adding to the pressure to find alternatives are new user tactical requirements and more demanding finish specifications. “So, on the one hand, you have all of these standards in place to deal with all of this, but DoD keeps running into the $10 to 20 billion annual expense in paint and corrosion. There is a vision that appliqué may be superior.”
What, exactly, would they be applying?
These plastic appliqués are made of fluoropolymers. Extremely tough, they display all of the nonstick, high-durability characteristics of their famous commercial version, Teflon™, a fluoropolymer compound. Plastic appliqués exhibit unique form-fitting characteristics, enabling them to be stretched to the contours of irregular surfaces more readily than, say, a sheet of normal adhesive plastic. The plastic coating “may not totally replace paint,” explains Brupbacher, but it is “so much more sophisticated that you get a much better film to begin with. Unlike a thin film that you paint on, you are always at a material science advantage when you can make something offline and then apply it.”
Think of paint as a skin coating that is designed to seal out corrosion and wear, as well as identify (or conceal) an object. Now think of a coating that can be applied at will and stripped off by hand, has coloring and patterning impregnated in it, and is tougher than paint—that’s Brupbacher’s vision. “One week I have to have my tank in Iraq. Next week, the jungle,” he says. “If I had an adhesive plastic that I could use to change the colors and camouflage, it would be much less difficult to apply and remove in the field. Something that can be handled that way points toward the superiority of appliqué.”
There are other advantages as well. “We are taking real plastics on the roll and putting nanoparticles in them,” Brupbacher explains. “The nanomaterials are not just smaller; they are different.
There are many kinds of threats out there, and there are many ways that nanomaterials might help meet them.” For security reasons, he doesn’t go into detail, but he will say that in today’s world of sophisticated surveillance, “detection” is no longer limited just to “the normal six senses. There are many things you can do to help yourself ‘hide’ in that world.” Appliqués embedded with certain nanomaterials can play a role in that effort.
Other potential applications for these high-tech films would be to protect aircraft from lightning strikes and to reduce drag. With paint, you can manufacture in anti-corrosion agents and tints. With polymer, there’s the potential of adding in materials to absorb radar; resist microbes; and function in harsh chemical environments, extreme temperatures, and supersonic speeds. Fluoropolymers can be useful in patching a bridge surface, protecting a metal roof, and even mimicking a metallic color.
Brupbacher came to Hopkins with broad and deep industry experience. He is using his knowledge and contacts to build a team of experts inside and outside of academia to further CMFA’s work.
The Center was established in spring 2003 through a three-year, $3.8 million research initiative funded by the Defense Advanced Research Projects Agency (DARPA). CMFA also is garnering support from branches of the military, the Johns Hopkins Applied Physics Laboratory, and others to explore the possibilities of appliqués.
To develop appliqué technologies, Brupbacher has teamed up with a small company, Integument Technologies, Inc., in Tonawanda, New York. Integument specializes in products to withstand extremes in temperature and chemical service environments. “Universities are not always equitable with small companies,” he says. “With Integument, we started with a different premise. We said, ‘We will work with you to help you, you can keep your intellectual property, and we can use our developments for other things.’ ”
It’s a win-win situation. “Integument gets what it needs for commercial markets,” explains Brupbacher, and the Center gets access to expertise and an outlet for its research. “This is a case where the tech transfer guys did it differently,” he says, “and it is bearing results.”