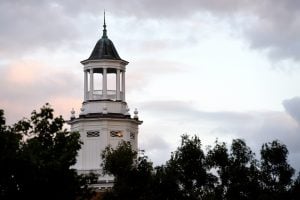
Wind turbines perched atop slender steel tubular towers have become a common site as the nation’s renewable energy infrastructure expands rapidly. These supporting towers, which have a diameter-to-thickness (D/t) of approximately 150 (and when taking into account how slender they are, sometimes as high as 300), are a remarkable feat of engineering. While the lightweight design of these thin-walled tubes can make them extremely efficient, in terms both of generating energy and their cost, imperfections that occur during the manufacturing process can leave them vulnerable to premature failure, a challenge that can result in manufacturers increasing the materials needed for construction.
Supported by grant from the National Science Foundation, a team co-led by Johns Hopkins University Professor Benjamin W. Schafer, director of the Ralph S. O’Connor Energy Institute and Associate Professor Michael Shields, an expert in uncertainty quantification, and CaSE alumnus and Northeastern University Professor Andrew Myers, an expert in wind turbine towers, are studying the link between the tower manufacturing processes and the structural behavior of these remarkable thin-walled tubes.
The fact that we don’t understand the nature of this relationship is a barrier to exploiting the true efficiency of these elements. Every bit of unnecessary steel we add into the towers takes away from our overall goals for a sustainable energy future,” says Schafer, the Willard and Lillian Hackerman Chair in the Department of Civil and Systems Engineering.
The grant is part of the NSF’s Grant Opportunities for Academic Liaison with Industry (GOALI) program and involves a collaborative study with the wind energy company Vestas. The study is a first of its kind, as it involves collaboration with Vestas experts and access to their Colorado wind turbine factory.
Access to the factory and its manufacturing process will help the team overcome one of the biggest impediments to understanding thin-wall tubular structures: the tubular elements used in civil infrastructure and mechanical systems are too large to be prototyped, iteratively designed, and tested at full-scale. Because of this, in the past, designers have had to estimate the elements’ structural strength, including the critical imperfects that can occur during manufacturing. The collaboration with Vestas now will enable the research team to move beyond estimation to directly measure full scale segments of the towers and develop precise information of the actual process.
“The ability of today’s non-contact measurement tools with access to directly measure tower geometric imperfections means we can develop a sizable database of measured imperfections. Combined with current simulation tools, this is exactly what engineers will need to reliably predict the strength of these towers as we push forward,” says Schafer.
This article originally appeared on the the Ralph S. O’Connor Sustainable Energy Institute site.