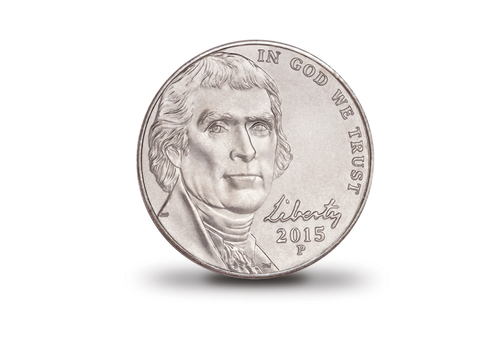
If Mark R. Stoudt has done his job well, you’ll never notice the change.
Stoudt MS ’92, PhD ’00 is a materials scientist at the National Institute of Standards and Technology and a member of the small team responsible for a new alloy expected to be used for the U.S. nickel.
It’ll look the same. It’ll feel the same. “That was the whole point of it,” Stoudt says. “[As a consumer], it’s one of those things where you don’t know what’s going on behind the curtain and you don’t care, as long as you put your coin in the vending machine and get the bag of chips.”
Around 2006, the nickel started costing more to make—just over 7 cents per coin—than it was actually worth, triggering the hunt for a less expensive replacement alloy. That’s a lot more challenging than it sounds; a striking variety of factors go into the makeup of the nickel. It has to have the right color. It needs to resist corrosion. It can’t be too brittle so it cracks when it’s struck, but it can’t be soft enough to wear away easily. It has to have a consistent weight. It even has to have the same electrical conductivity, because that’s how vending machines identify it.
The U.S. Mint turned to NIST’s Materials Measurement Laboratory to investigate the solution. Over the course of three years, Stoudt, metallurgist Carelyn Campbell, and materials research engineer Eric Lass used a combination of computer modeling and measurements of material properties to come up with the best possible alloy while saving 25 to 40% on the current cost of the coin. Four patents arose from the work, and in December, the group was awarded the U.S. Department of Commerce Bronze Medal.
Stoudt has been with NIST since 1986, starting there shortly after earning an ASE in chemical engineering and a BSE in metallurgical engineering from Penn State. He would later attend Johns Hopkins to obtain both his MSE and PhD. “I wanted to be a chemical engineer back in eighth grade,” he recalls. “It’s one of those things where research gets into your blood and you’re trained to attack a problem a certain way, and you start acquiring skills. I’m not doing anything directly related to my PhD research, but the skills I learned are applied on a daily basis.”
Stoudt is currently working on projects involving additive manufacturing processes, or 3-D printing. The technology “has opened up areas of design space that were off-limits until a few years ago,” he says.
But Stoudt looks back fondly on his days with the nickel. “It was fun to work on. I learned more about the interplay of these characteristics and how it relates to what I would be testing,” he says. “You’re always learning.”