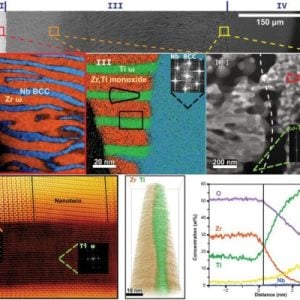
Materials scientists at Johns Hopkins have supercharged the hardness of a material used in high-temperature environments, moving it one step closer to use in jet engines, rocket propulsion, nuclear fusion, and orthopedic implants.
Led by Mitra Taheri, professor of materials science and engineering at the Whiting School of Engineering and director of its Materials Characterization and Processing (MCP) facility, the researchers made their discovery while trying to improve the ability of refractory multi-principal element alloys (RMPEAs)—materials made of a mix of metals in nearly equal amounts—to resist oxidation, or rusting in high temperature environments. What they found was that the physical properties of the alloy improved after the typically detrimental process of oxidation. Their findings appear in Science Advances.
“Previous research suggests that metal alloys become brittle and break easily after oxidation,” says team member David Beaudry, and PhD student. “When we added oxygen to RMPEAs, we found that the alloys grew significantly harder without sacrificing their toughness.”
Initially, the team set out to identify how oxygen impacts the alloy. After exposing the alloys to temperatures of 2000 degrees Fahrenheit, they employed the MCP’s Focused Ion Beam (FIB) microscope—which uses a stream of ions to image, cut, and remove microscopic slivers of materials for high-resolution analysis. They then used the MCP’s Transmission Electron Microscope (TEM)—which uses an electron beam to image and analyze miniscule samples at the atomic level. Collaboration with the U.S. Naval Research Lab allowed the team to perform atom-probe tomography (APT) on the FIB samples, showing 3D models of atoms inside the alloy.
“After the alloys were removed from the heat, we saw interesting structures develop in the sample,” says Beaudry. “We used the FIB to extract minute samples, then used TEM and APT analysis to try and understand at the atomic level what was happening under high temperatures,” he says. Collaborators on the project from Northwestern University ran computer simulations that matched the team’s observations.
The result surprised them: Instead of the material essentially rusting away, it became harder and didn’t lose its toughness.
“The materials’ hardness increased almost 7 times after taking up oxygen, forming new structures called hierarchical heterogeneities. These nanoscale structures change the alloy to be firm but flexible, so they maintain their strength and don’t crack under pressure,” says Beaudry.
With their discovery, researchers can refine future RMPEAs and figure out how to keep them tough and stable.
“We’ve uncovered what causes the atoms to restructure when oxygen is added to RMPEAs. We can apply these same thermodynamic parameters, select other elements to add into these alloys in very small amounts, and hopefully find that the hardness increases alongside oxidation resistance while maintaining toughness and overall resiliency,” says Beaudry.
The team aims to find the perfect balance: preserving the alloy’s chemical stability while it expresses physical resistance to external forces. Their conclusions could enable the development of a durable alloy that withstands oxidation and fractures.
“This discovery gets us one step closer to implementing RMPEAs in extreme environments, from space to the human body,” he says.
In addition to collaborators previously mentioned, Beaudry and Taheri also teamed up with researchers from The University of Maryland, Columbia University, The University of Virginia, The University of California-Irvine, and the French National Center for Scientific Research (CNRS) to analyze and publish these findings. This project was funded by the Office of Naval Research (ONR).
This article first appeared on the Johns Hopkins Department of Materials Science and Engineering website.